Healthcare Waste Service Contingency Planning
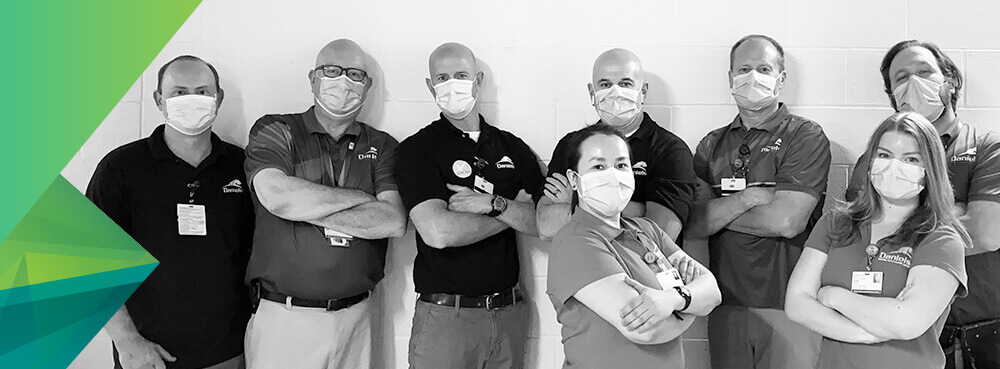
Hospital Waste Management Services in a time of COVID-19 has been put under immense strain, but as our “world as normal” is becoming closer to grasp, we wanted to look back and recognize both the commitment and foresight of our staff and the vision of our leader, Dan Daniels, in being prepared to go above and beyond even when it came at deep personal and commercial cost.
TOPICS WE WILL COVER:
1 / Daniels Service Response during the Pandemic
2 / Daniels Contingency Planning
3 / Hospital Waste Management Service Continuity
Daniels Service Response during the Pandemic
WHO has been assessing this outbreak around the clock and we are deeply concerned both by the alarming levels of spread and severity, and by the alarming levels of inaction. We have therefore made the assessment that COVID-19 can be characterized as a pandemic.11th March 2020 | WORLD HEALTH ORGANIZATION
Within days of this announcement, our world was changed. In the United States, elective surgeries stopped almost overnight, general practices went virtual, and our teams broke out into war-room style decision sessions to prepare for the worst. Servicing over 8000 healthcare facilities across the United States, we had to ensure that every aspect of our operations and customer support was prepared for the changes a pandemic would bring.
On the 18th March our founder and CEO addressed the healthcare community with a promise.
"we are collectively here for you."
In the ensuing months, our team “did us so proud”:
- Individuals stepped up to take on new responsibilities and cross-functional roles, even travelling to different business units to offer support
- Our Chicago support team put on their khaki’s and over the course of 3 weeks ran a significant socially-distanced installation of Daniels containers across the entire RUSH University Health System
- We scaled our services to meet customer demand, handling surge volumes and even supported non-customers when their vendors couldn’t maintain service.
- We responded overnight to new satellite COVID-19 vaccine center setups with staff working through the night to make way for patients
- Our Drivers and Production Workers took on additional shifts and routes to support with surge volumes
- Our support teams banded together to redefine how departments supported our colleagues in a virtual landscape
- We explored community in new ways – significant milestones, promotions, happy hours and team love.
While all of these things were meaningful however, the definition of true success for our collective teams was being there for our healthcare partners. During the pandemic, our teams achieved a service success rate of 98.75%; in a service industry with hundreds of variables, that number is astonishing and a real tribute to our drivers, our process workers, and our leadership.
Responding to customer needs, national pandemic protocols and CDC guidelines, Daniels Health was able to not only minimize disruption to its services during COVID-19, but delivered increased supply and operations nationally to accommodate US Healthcare’s altered landscape. Furthermore, our Sharpsmart container was used for the first publicly administered covid-19 vaccine in the world
Daniels Health Contingency Planning
Understanding that our services directly support the frontlines of healthcare, in the event of a national pandemic we deploy contingency planning across every facet of our business to ensure service, customer support and supply chain consistency. Through this last 12 months we deployed additional resources, stock and services to support healthcare during its time of need, this included:
1 / Service Continuity
Daniels operates a network of processing plants and transfer stations across the USA. This network provides contingency options in the event a plant becomes inoperable ensuring continuity of service. Nationally across Daniels’ 21 operational facilities we were able to maintain “business as usual”, accommodating both current and additional service routes, increased container stock levels, and partnering with hospitals to align our service technician program with changed hospital protocols.
2 / Enhanced Stock Levels
Daniels carries a contingency stock holding of bins and containers both at a local plant level and in our national warehouse which was able to be called upon to accommodate rapid surges in waste containment demands. Our supply chain is managed in the US with local manufacturing to ensure timely responsiveness.
3 / Manufacturing and Supply Chain
Manufacturing dependency is mitigated by Daniels owning their own set of tools required for the manufacture of sharps and other healthcare waste containers. Outsourcing supply to a number of local manufacturing facilities in Michigan further mitigates reliance on any single manufacturing arrangement.
4 / Staffing Contingencies
Daniels employed surplus labor to account for any shortages (supported by our inhouse recruitment team) with temporary labor replacement that could be deployed within 24 hours. Our national network of management support and cross-trained labor was redeployed to areas most affected. Daniels internal training processes, SOPs and standardized operational procedures across all of our business units enabled fast effective onboarding, cross-functional support and workforce continuity effectiveness.
5 / In-Hospital Service and Virtual Support
Our national service technician program was able to maintain not only existing service levels but also accommodate additional hours required. Our in-hospital service technicians were trained to follow each facility’s specific infection control practices (including new protocols for entering isolation rooms), and provided with appropriate PPE. Our Account Management team supercharged their support to hospitals both in person and virtually, delivering fast-tracked logistical, product, storage and training workarounds to changing needs and protocols driven by the pandemic.
6 / Education and Waste Segregation
Leveraging our inhouse compliance and education experts we deployed education, customer training and point-in-time communications (in accordance with instructions provided by the CDC and other regulatory authorities) advising on correct waste segregation protocols, and supporting healthcare facilities to reduce their risk of cost spikes by over-classification of COVID waste.
Hospital Waste Management Service Continuity
COVID-19 has forced an examination of clinical hygiene practices both inside and outside of the healthcare environment and at no time in these last two decades has Daniels’ clinically differentiated services and container-cleanliness approach been more universally recognized. However what has also been recognized particularly for hospitals, is the importance of a medical waste partner that is able to overcome disaster-challenges to maintain quality and reliability of service and support health care continuity.
As a hospital medical waste management partner, these are the imperatives that our team and our company stand by:
- Reliable waste management pickups
- Adequate container stock and tight supply chain to support with contingency situations
- Responsiveness and agility when the needs of our customers change (even overnight!)
- Proactive communications with issue escalation procedures that go right up to our CEO
- The same service excellence experience for every facility, from a dentist or surgery through to a hospital system