UVA University Hospital
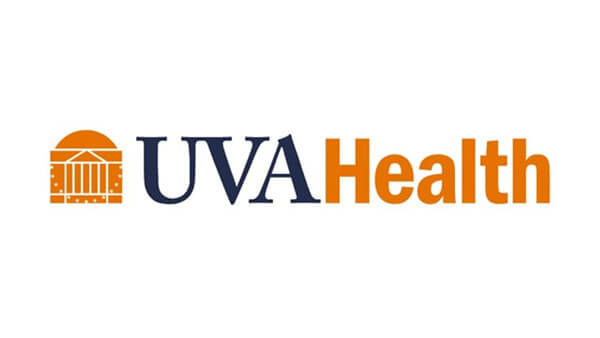
The Challenge
UVA University Hospital, a 700-plus-bed acute care facility within the UVA Health System, historically utilized disposable containers to manage their sharps waste. However, when a catastrophic fire disrupted their supplier’s ability to deliver containers, UVA suddenly found themselves facing a potential severe impact to hospital service continuity.
Unable to function within the parameters of the existing waste service agreement, UVA Health put out an urgent request for information (RFI) for medical waste disposal vendors with an accelerated transition timelines critical for success. Daniels was one of four regulated medical waste disposal vendors to respond to the RFI.
Our Approach
STEP 1
Site Assessments
Within one week of the RFI, Daniels Health sent a team to UVA to investigate the facility’s needs over the course of a two-day site assessment. This comprised of department-level audits within the hospital to evaluate the current disposal process, speaking to key stakeholders across teams and gathering insights to inform the installation plan.
This first phase was critical to understanding UVA’s specific requirements. By working directly with UVA staff within their facility, Daniels could develop an installation plan that minimized disruption to patient care while emphasizing a smooth, seamless transition.
STEP 2
Developing an Installation Plan
Following the on-site visits, Daniels had a week to develop a comprehensive installation plan. As part of this process, the installation team collaborated with the hospital’s infection control & prevention team (ICP) to address concerns around dust created during the installation. This resulted in an agreement to use HEPA filtered drills and bit cleaning systems.
While other vendors estimated an 8–10-week transition timeline, the installation plan delivered by Daniels committed to a three-week installation process.
With the guarantee of a faster turnaround time and a dust-free process, Daniels was ultimately approved to move forward with installation in all locations, including rooms with patient occupancy.
STEP 3
Installation
Rather than relying on locally-sourced, temporary laborers, the Daniels installation process is completed by our full-time installation team, ensuring a high degree of competence, capability, and know-how.
Daniels began the installation process with an all-hands-on-deck approach, bringing in additional team members to support with unloading of pallets, removal/disposal of existing full sharps containers, and clearing away miscellaneous boxes and trash. This enabled the installation team to focus on their primary task.
Given the container supply issues driving this transition, the installation team focused first on some of the most difficult units in the facility to ensure service continuity in these critical areas. On the first night of the installation, Daniels transitioned the PICU, which had a full census and three severely ill patients. The PICU team members were thrilled with the results and quickly spread the word to other departments concerned about potential disruptions.
The rest of the installation continued apace, with the installation team taking advantage of their situational experience to find opportunities to speed up the process. By exhibiting flexibility in their approach while respecting the hard-scheduling limits of certain departments, the team was able to improvise as needed to deliver ahead of schedule.
The Solution
Thanks to the extensive pre-planning, as well as the installation team’s flexibility and high level of experience, the installation was completed earlier than expected. The average time for a full exchange was approximately four minutes for a wall-mounted unit and 30 seconds for a stand-alone bin.
The speed and efficiency of the transition enabled the team to address additional punch list items as well as providing supplementary education to clinical and EVS staff on compliant disposal processes.
The Outcome
UVA Health was incredibly pleased with the installation process, praising Daniels’ ability to deliver above expectations despite an urgent, time-sensitive process. In recognition of this achievement, the UVA leadership honored our team with the creation of a scholarship in the name of Daniels Health.
The donation noted that it “was made in recognition of exceeding excellence in workmanship, teamwork, leadership, and professionalism exhibited by [Daniels Health].” The entire Daniels Health team is proud to support the education of a young woman thanks to this scholarship.
In addition to this unexpected honor, the UVA team has provided significant positive feedback from their clinical and EVS staff after using our containers:
- Team members feel safer owing both to the size and openness of the containers’ receptacle and the sealed top. No more assembly of top covers onto the collection bin using plastic clips that break or fall apart.
- Team members feel that the system is cleaner – no more cabinets to sanitize between patients.
- Team members appreciate the flexibility of the system to flex up another size if their units are getting too full too fast using the universal bracket.
-
Team members appreciate having the extra capacity.
UVA Health project manager Michael A Payne, MHA, summed up the success of this installation succinctly when asked to provide his personal observations: “In a word, expect exemplary customer service from the installation team.”